How to deal with the problem or blockage in the brewing group of the coffee machine? Basic troubleshooting methods of coffee machine
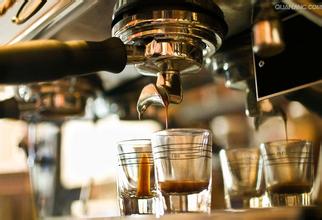
Abstract: coffee machine installation-maintenance-maintenance-after-sales part: this paper mainly introduces the Chinese translation of English display of some common faults encountered in coffee machine, as well as the troubleshooting methods and other related knowledge points.
1. Trouble Tips and troubleshooting methods of Coffee Machine in English
Many high-end fully automatic coffee machines have a display screen, most of which are displayed in English because of technology and various reasons. It is especially a headache for domestic coffee machine users. Here, we will provide you with the English display and troubleshooting methods of some common coffee machine failures.
BREW UNIT BLOCK
There is a problem or obstruction in the brewing group. Need to clean and check and return to position.
BREW UNIT MISS
There is an error in the brewing group. Not installed or the service door is not closed.
COF. BEANS EMPTY READY FOR USE
No coffee beans, add coffee beans and restart the machine.
DESCALE READY FOR USE
The bean dregs tank is full. Clean up the bean dregs trough.
DREGDRAW MISS
The coffee residue box is not in place and jammed tightly.
DREGDRAWER FULL READY FOR USE
The bean dregs tank is full. Clean up the bean dregs trough.
ENERGY SAVING
Power-saving device activated, standby. Just press ENTER gently.
FELL COFFEE BEANS READY FOR USE
No coffee beans. Restart the machine after adding coffee beans.
FILL WATERTANK
There is no water in the tank.
GRINDER BLOCKED
There's something wrong with the bean grinder. Need to clean the bean grinder, or contact the maintenance personnel.
OVER TEMPERATURE
Let the machine drain again.
VENTILATE
If there is no water in the water tank or internal waterway, drainage must be done before the boiler is heated.
WARMING UP
When heating the boiler, wait about 3-5 minutes until "SELECT PRODUCT" and "READY FOR USE" are displayed.
two。 What if the filter of the coffee machine is blocked?
Just rinse the strainer.
Cleaning of filter screen
1. Use the handle of a spoon against the edge groove of the filter (do not use a sharp instrument) and pry down at different angles until the filter falls off. (the same method on the left and right)
two。 Put the filter screen, sealing ring and cannon handle into a clean slag tank, add 30 grams of special cleaning powder for coffee machine, then soak in 900 ml of boiling water for 20 minutes, then rinse with clean water.
3. After washing the filter screen, sealing ring and gun handle with clean water, put it into a clean slag tank, soak it with boiling water for one night, and install it on the brewing head the next day.
Note:
For the installation of the brewing head, put the sealing ring up on one side of the word, put it flat on the filter net, then put it into the handle strainer of the brewing head, and finally install the handle straight on the brewing head. (do not tilt, straight and hard to the top, counterclockwise needle rotation handle)
3. Basic troubleshooting methods of coffee machine
1. The machine has no power: 1. Whether the machine power switch is turned on or not. 1. Turn on the machine power switch. 2. Whether the power supply switch is on or not.
2. Check the power supply switch and find a professional if you want to.
3. Whether the power connection is correct or not. 3. Check the power connection
2, boiler water shortage: 1, external water supply is off 1, check external water supply 2, machine automatic water supply system is not turned on 2, turn on machine water filling system 3, filter blockage 3, replace filter element 4, pump motor card main 4, check pump 5, pump motor fuse 5, check fuse
3. Too much water in the boiler 1, too dirty solenoid valve into the boiler 1, cleaning or replacing the solenoid valve
2, heat exchanger perforation 2, if possible, replace heat exchanger 3, water level probe or weak ground contact is not good 3, reconnect
4. no steam in the steam nozzle 1, raise the water level of the boiler 1, check the water supply system
2. the pressure switch is broken. 2. Replace the pressure switch.
3. Problems with the heating safety device 3. Check the heating safety device (if any)
4. Nozzle blockage 4. Clean up
5. Coffee cannot be extracted 1. Water shortage in the system 1. Check the water supply system.
2. Head solenoid valve damage 2, replacement head solenoid valve 3, pump jam 3, check pump 4, control fuse burn 4, replace fuse 5, nozzle clogging 5, cleaning nozzle 6, head solenoid valve clogging 6, cleaning head solenoid valve
6. Machine leakage 1, drainage pipe clogging 1, cleaning drain pipe
2. Break the water pipe. 2. Replace the drainage pipe.
7. Low espresso temperature: 1. Burnout of electric heating rod. 1. Replacement of heating rod.
2, wire connection error 2, check wire connection 3, too much scale in heat exchanger 3, descaling
4. Pressure switch aging 4, change pressure switch 5, thermal cycle blockage 5, check thermal cycle
8, espresso temperature is high: 1, the pressure switch is adjusted too high 1, adjust the pressure switch
2. Coffee powder is too fine. 2. Adjust the size of the grinding powder.
9, coffee flow rate is too fast: 1, coffee powder is too coarse 1, adjust the size of the grinding powder
2. The machine temperature is too high. 2. Check the machine temperature
10, the coffee flow rate is too slow: 1, the coffee powder is too fine 1, adjust the grinding powder thickness
2. Handle filter cup is too dirty 2, cleaning filter cup 3, head solenoid valve blocking 3, cleaning or replacement 4, internal blocking of machine head 4, checking head assembly 5, nozzle blocking 5, cleaning nozzle
11, coffee powder is too wet: 1, the head solenoid valve is not closed tightly 1, check the solenoid valve
2, the temperature is too low 2, waiting for the temperature to rise to the standard value 3, coffee powder is too fine 3, adjust coffee powder thickness 4, thermal cycle blockage 4, check thermal cycle
12. The pressure gauge can not display the pressure correctly. 1. The display position of the pressure gauge is incorrect. 1. Change the pressure gauge
13 all panel lights flashing: 1, do not add water within 2 minutes 1, check the water supply system
2. No water in main pipe 2, check machine pipe 3, Sheung Shui system off 3, check filter, 4, filter blockage 4, check probe and weak connection 5, weak connection virtual 5, check probe and weak connection
14. Incorrect extraction
Coffee quantity is different from setting 1, coffee powder quantity is incorrect 1, check bean grinder quantitative distributor 2, Flowmeter connection is incorrect 2, check connection
3, the electrical part has water 3, the drying electric control department 4, the Flowmeter is broken 4, replace the Flowmeter
15. Only manual switch works: 1. Computer board fuse burns out. 1. Replace fuse.
2. Connection error 2. Check the connection
16. Pump works only when manual extraction: 1. Pump fuse burns out. 1. Replace fuse.
17, pump leakage: 1, seal damage 1, replacement of pump head
2. There is no loosening at the entrance and exit. 2. Maintenance. 3. Adjustment nut loosening. 3. Maintenance.
Source: network
- Prev
What is the coffee partner added to coffee? Can you replace it with milk and sugar?
Yes. The main ingredient of coffee mate (commonly known as creamer) is plant fat powder. Vegetable fat powder is a general term for vegetable fat powder. Vegetable fat powder has a wide variety of functions and applications. Its production history can be traced back to the 1950s. It has been widely used in baked food ingredients, cold food ingredients, confectionery ingredients and solid beverage ingredients. Use creamer (milk) in coffee
- Next
Key points of coffee knowledge: what is the difference between an Italian coffee maker and an American coffee maker?
Coffee machine is the general name of a kind of coffee brewing machine, which is divided into American style and Italian style. Many people do not know much about the difference between Italian coffee machine and American coffee machine. Today, the editor of Wang Sen Coffee training School has experienced a coffee trip according to their differences. The content is rich, and there are all kinds of shopping skills. Brand models are not recommended to avoid the suspicion of advertising. Italian coffee
Related
- What is the meaning of lactic acid fermentation with coffee bean treatment?
- How to judge the state of foam by sound?
- How does the latte pull out the unicorn pattern? Come to get for a little trick to improve the flower pull!
- Will flower pulling affect the taste of the latte?
- Do you know the history of coffee?
- The difference between honey treatment and sun washing what is raisin honey treatment?
- What kind of milk can a novice use to make coffee foam to keep the foam longer? The correct method and skills of milking tutorial sharing
- Why do washed coffee beans taste sour? Flavor characteristics of washed Coffee
- Introduction to the skill of how to practice the size and height of water injection around the circle of hand-brewed coffee
- How do beginners practice coffee flower drawing from scratch?